AQL Sampling Inspection Explained: How to Read Tables and Design a QC Plan
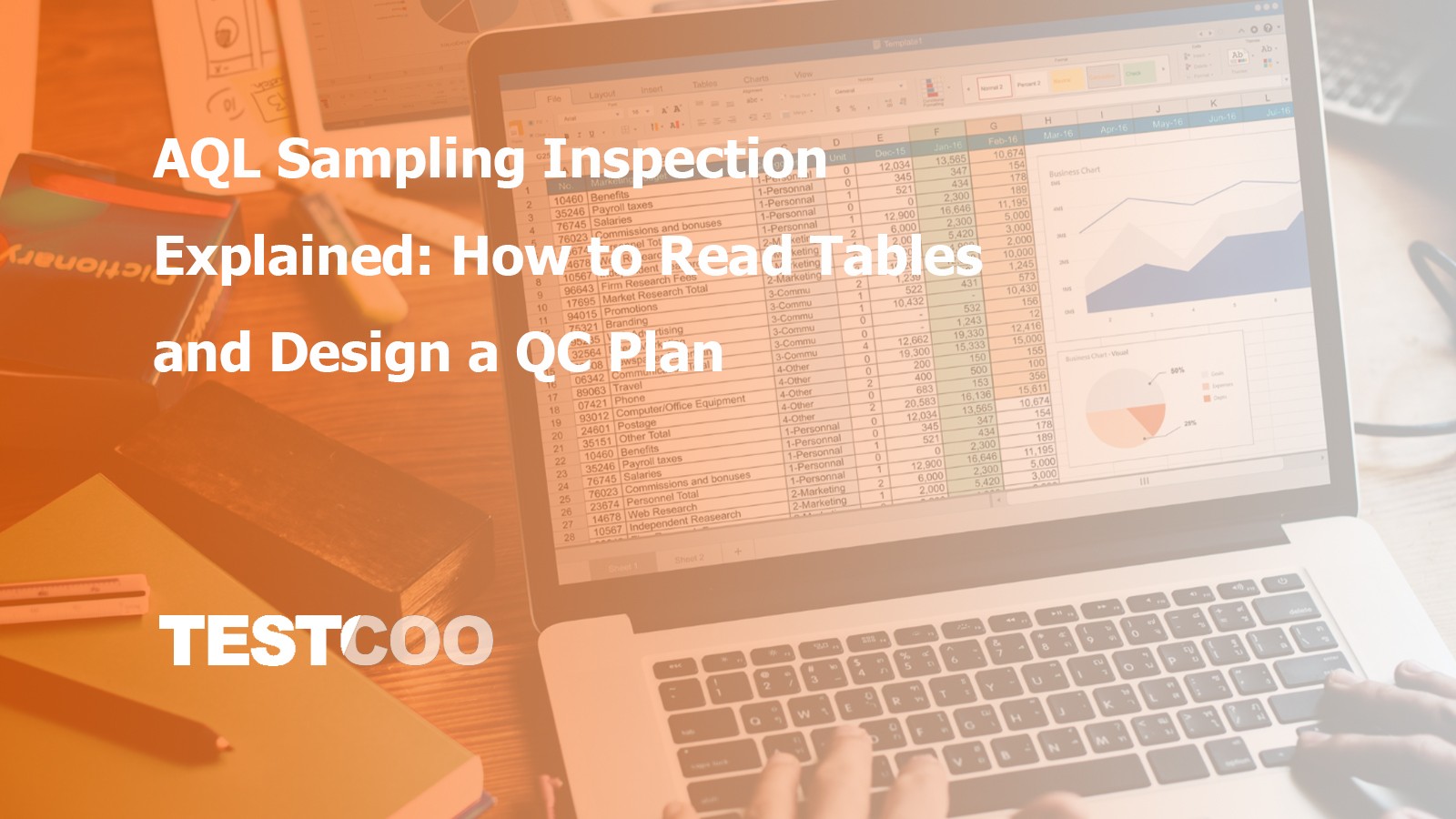
In global manufacturing, where product quality can make or break a brand, AQL (Acceptable Quality Limit) sampling inspection remains one of the most widely used methods for ensuring standards are met without the need to check every unit. Imagine you're a buyer overseeing production in another country — thousands of units are being made, but inspecting each one is costly and time-consuming. How do you strike the balance between efficiency and risk?
This is where AQL sampling comes in. It offers a structured, statistical approach to quality control that helps businesses make informed decisions — whether to accept or reject a lot — based on a sample size. But for many, the AQL tables and codes can look confusing at first glance.
In this article, we’ll break down what AQL really means, how to read the tables step-by-step, and most importantly, how to design a QC plan that fits your product, budget, and risk tolerance. Whether you're a sourcing manager, supplier, or simply curious about how quality is measured at scale, this guide will simplify AQL for you.
What is AQL?
AQL (Acceptable Quality Limit) sampling inspection is a statistical tool for quality control, primarily used to determine whether a batch of products can be accepted or rejected.
What is the Use of AQL Sampling Inspection?
AQL sampling inspection is mainly applied in mass production. By inspecting a portion of products in a batch, it infers whether the quality of the entire batch meets the requirements. The core idea of the AQL sampling method is that there is no need to inspect every product; instead, the quality level of the entire batch is estimated through sampling inspection of some products, thereby saving costs and time.
Standards for AQL Sampling Inspection
The AQL (Acceptable Quality Limit) sampling standards include:
ANSI/ASQC Z1.4
Developed jointly by the American National Standards Institute (ANSI) and the American Society for Quality (ASQ), its full name is "Sampling Procedures and Tables for Inspection by Attributes".
MIL-STD-105E
A sampling inspection standard formulated by the U.S. Department of Defense, with the full name "Military Standard 105E - Sampling Procedures and Tables for Inspection by Attributes".
BS 6001
Issued by the British Standards Institution (BSI), its full name is "BS 6001 - Sampling Procedures for Inspection by Attributes", used for implementing sampling inspection in production and manufacturing processes.
ISO 2859
A set of quality management standards developed by the International Organization for Standardization (ISO), with the full name "Sampling Procedures for Inspection by Attributes", aiming to provide guidelines and procedures for attribute-based sampling inspection.
Read More: Understanding ISO 2859
GB/T 2828.1
A Chinese national standard, officially named "Sampling Procedures for Inspection by Attributes - Part 1: Sampling Schemes for Lot-by-Lot Inspection Indexed by Acceptable Quality Limit (AQL)". It provides enterprises with a set of quality control procedures based on sampling inspection, applicable to quality inspection in mass production.
Read More:AQL Table | How to Read It
How to Read AQL Sampling Standard Tables?
Table 1: Sample Size Code Letters Table
This table is used to determine the sample size code letter based on the lot size and inspection level.
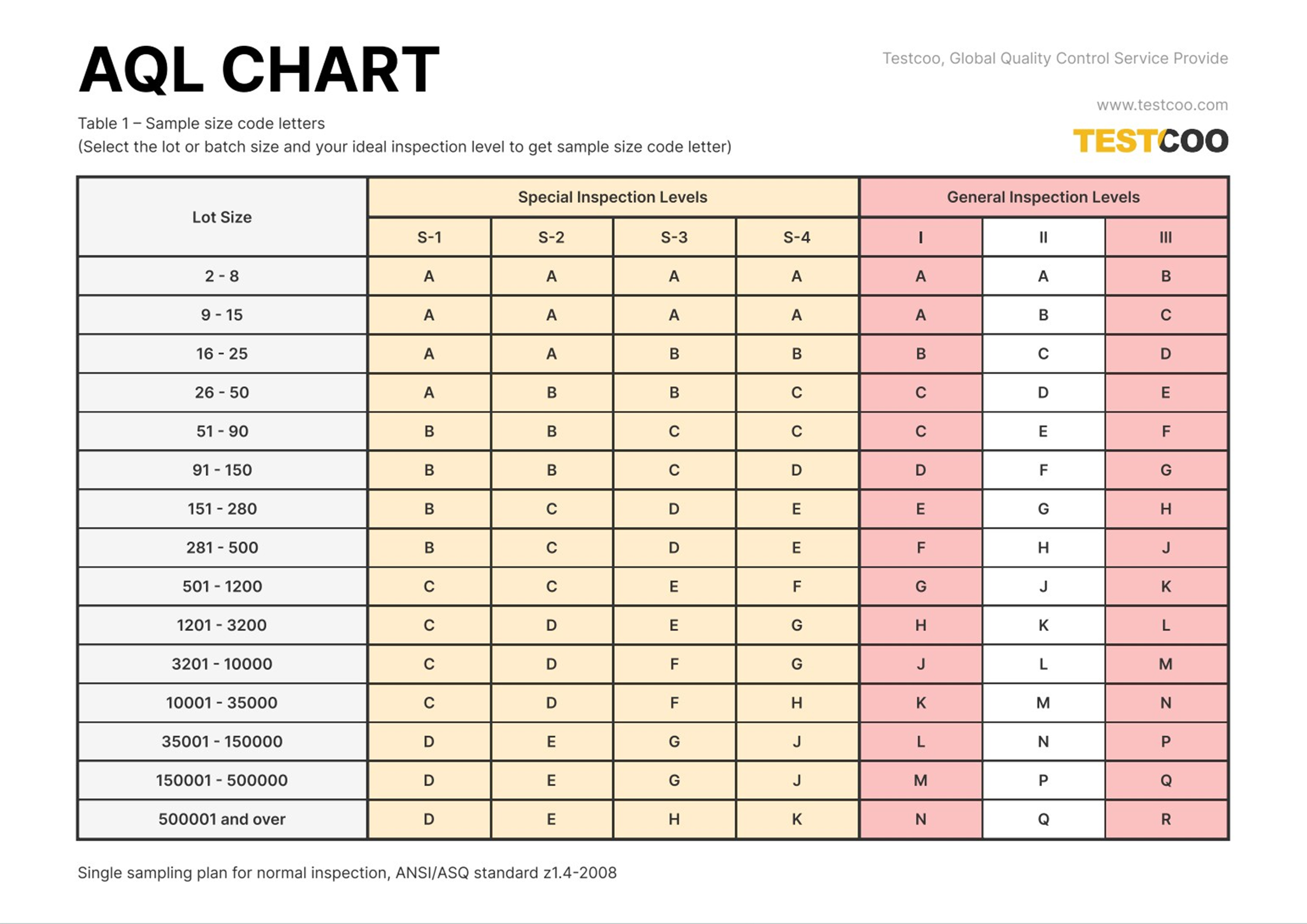
???
- Lot Size:The number of units in the batch to be inspected, listed in the first column of the table.
- Inspection Levels:
- Special Inspection Levels: Divided into "S-1", "S-2", "S-3", "S-4", with discrimination ability: S-1 < S-2 < S-3 < S-4.
- General Inspection Levels: Divided into "I", "II", "III", with discrimination ability: I < II < III.
- Generally, general inspection levels are more discriminative than special inspection levels.
???????Principles for Selecting Inspection Levels:
- If not specifically specified, general inspection level II is used first.
- Consider inspection costs: If the cost of inspecting a single sample (a) is greater than the cost of handling a non-conforming batch (b), choose level I; if a = b, choose level II; if a < b, choose level III.
- To ensure AQL and minimize the risk of accepting substandard batches, choose a higher inspection level.
- Choose a higher inspection level when inspection costs (including labor, materials, time, etc.) are low.
- Choose a higher inspection level when product quality is unstable or fluctuates significantly.
- Choose a lower inspection level for destructive testing or testing that severely reduces product performance.
- Choose a lower inspection level when inspection costs are high.
- Choose a lower inspection level when product quality is stable and has small differences.
- For trial products with little or no historical data, or products produced intermittently, choose a higher inspection level for safety.
- Application Scenarios for Special Inspection Levels:
- Destructive testing of products.
- Products with high intrinsic value.
- High inspection costs.
- Usage Method:
Find the corresponding sample size code letter by locating the intersection of the lot size and the selected inspection level in the table.
Example: For a lot size between 1201 and 3200 units and inspection level II, the corresponding sample size code letter is K.
Read More: How to Read AQL Table?
Table 2: Single Sampling Plans for Normal Inspection
This table is used to determine the acceptance and rejection criteria based on the sample size code letter and AQL value.
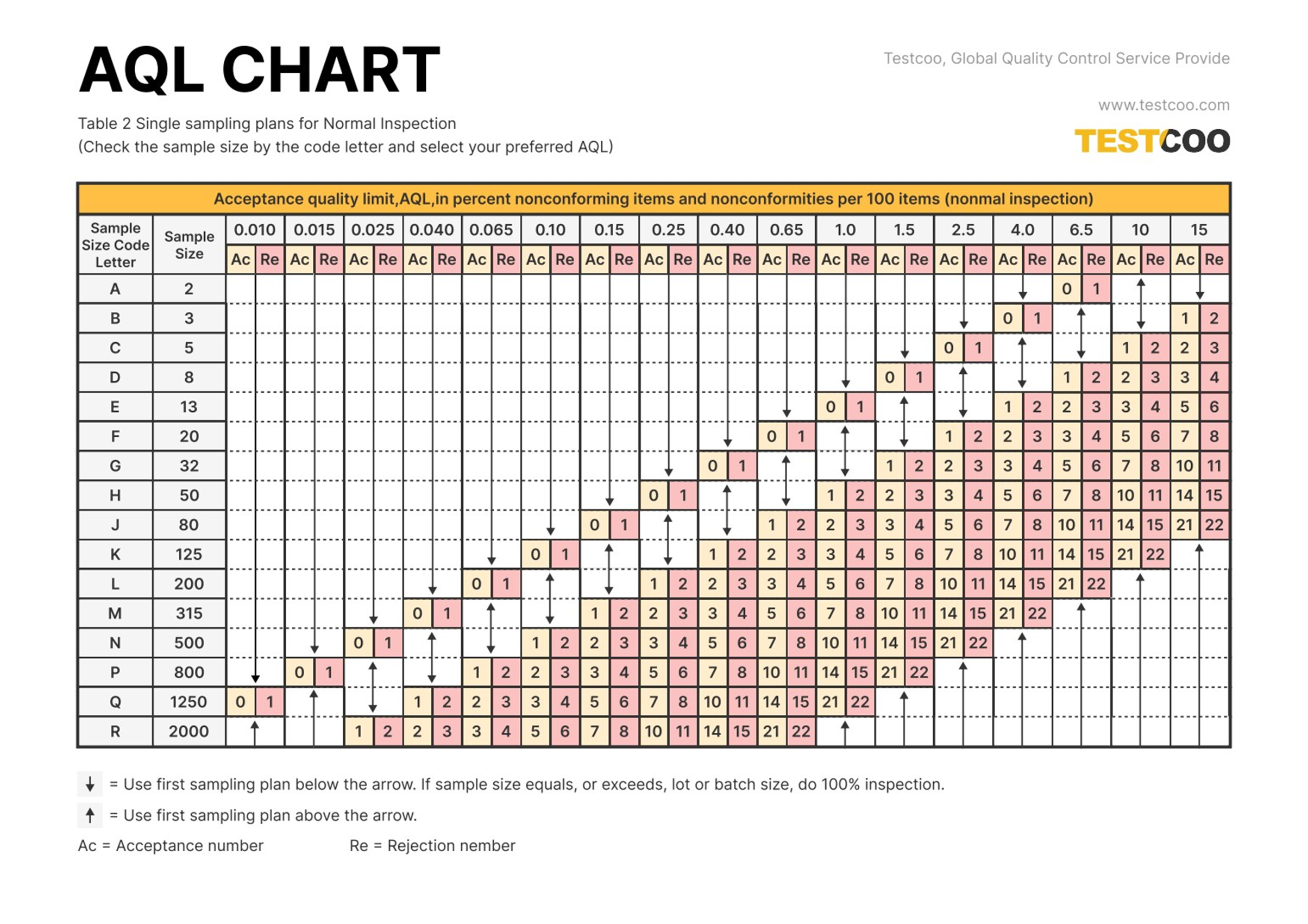
- Sample Size Code Letter: Corresponds to the code letter obtained from Table 1.
- Sample Size: The number of samples to be inspected, determined by the sample size code letter from Table 1.
- AQL Value: A series of numbers (0.010, 0.015...6.5, 10, 15), with 21 grades in total. A lower AQL value indicates higher quality requirements.
- Ac (Acceptance Number) / Re (Rejection Number): The maximum number of defects allowed for acceptance (Ac) and the minimum number of defects that result in rejection (Re). If the number of defects in the sample is ≤ Ac, the batch is accepted; if it is ≥ Re, the batch is rejected.
- Usage Method:
Using the sample size code letter from Table 1 to confirm the sample size, then find the corresponding Ac and Re based on the AQL value.
Example: If the sample size code letter is K, the sample size is 125. Assuming AQL is set to 2.5% for major defects and 4.0% for minor defects:
- For major defects (2.5%), the batch is accepted if the number of defects is ≤ 7; rejected if > 7.
- For minor defects (4.0%), the batch is accepted if the number of defects is ≤ 10; rejected if > 10.
How to Design an AQL Sampling Inspection Plan?
Step 1: Confirm Known Conditions
Obtain three essential conditions in advance:
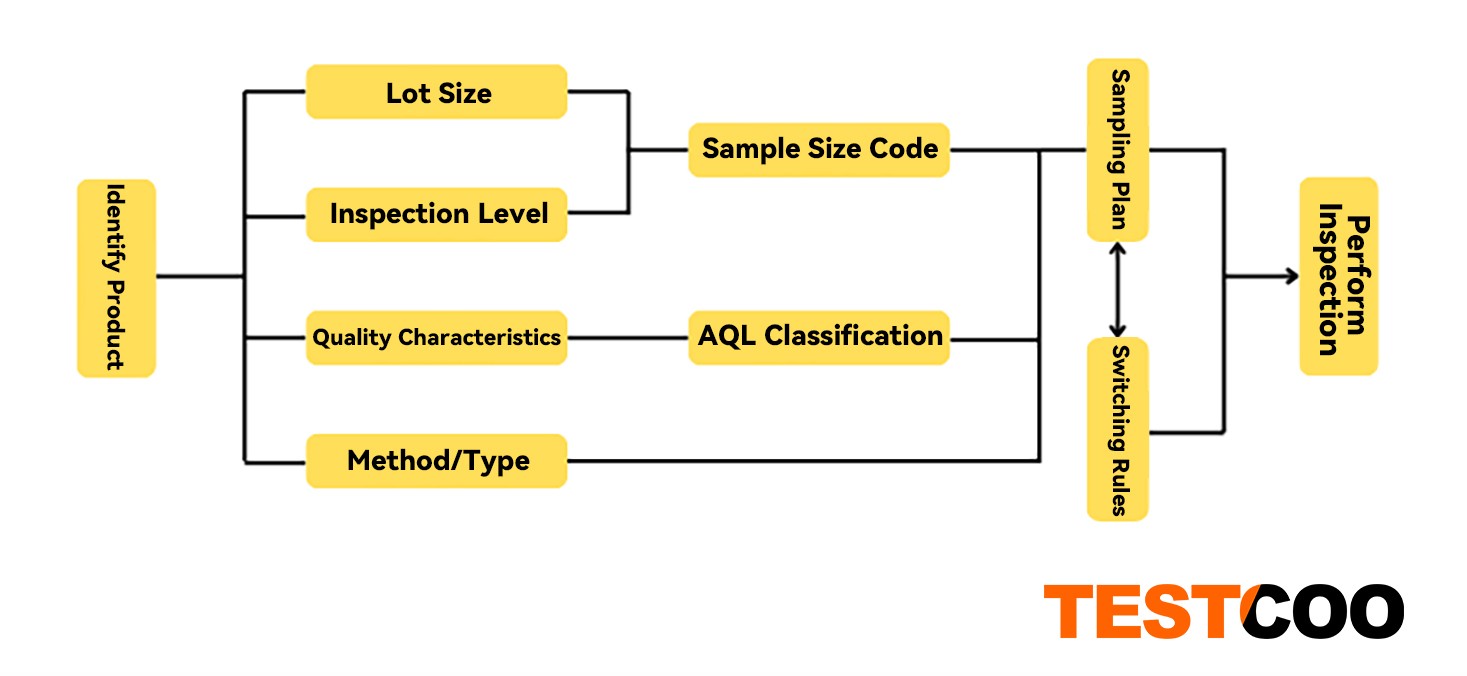
- Lot Size: The total number of products to be inspected (obtained from the order).
- Inspection Level: Confirmed in advance by the manufacturer and the buyer (brand owner) before placing the order.
- AQL Value: Confirmed in advance by the manufacturer and the buyer before placing the order.
Step 2: Determine the Sample Size Code Letter
Use the lot size and inspection level to find the corresponding sample size code letter in Table 1 (Sample Size Code Letters Table).
Step 3: Confirm the Sample Size
Find the sample size corresponding to the sample size code letter in Table 2 (Single Sampling Plans for Normal Inspection).
Step 4: Determine Acceptance and Rejection Criteria
Combine the sample size with the AQL value to find the corresponding Ac (acceptance number) and Re (rejection number) in Table 2.
Tips
Defect Types:
- Critical Defects: Defects that may cause harm or unsafe conditions to consumers during use or maintenance, violate relevant laws and regulations, or damage the key/ultimate basic functions of the product.
- Major Defects: Functional defects that reduce product usability and reliability without affecting safety, or obvious appearance defects that affect sales.
- Minor Defects: Defects that do not significantly reduce the expected performance of the product, or deviations from standards that only slightly affect effective use/operation but may affect sales.
- Note: If multiple defects are found in one product, only the most serious defect is counted in the defect count, but other defects should be noted. Any critical defect results in the entire batch being rejected, with acceptance determined by the customer.
- Default Sampling Plan:
The default sampling plan is level II inspection, with AQL acceptance criteria: critical defects (not allowed), major defects (2.5%), minor defects (4.0%). These values can be adjusted based on product type or the relationship between the buyer and manufacturer.
- Arrow Symbols in AQL Tables:
If an arrow is encountered, use the Ac/Re values in the direction of the arrow and reselect the corresponding sample size. If the sample size is equal to or exceeds the lot size, conduct 100% inspection (applicable only to a single defect level).
Read More: A Complete Guide Understanding AQL in Product Inspections
Example of an AQL Sampling Inspection Plan
A company orders 13,000 suits from a Chinese clothing manufacturer (single batch production). The agreed AQL levels are: critical defects (0.0%), major defects (2.5%), minor defects (4.0%); inspection level is general level II.
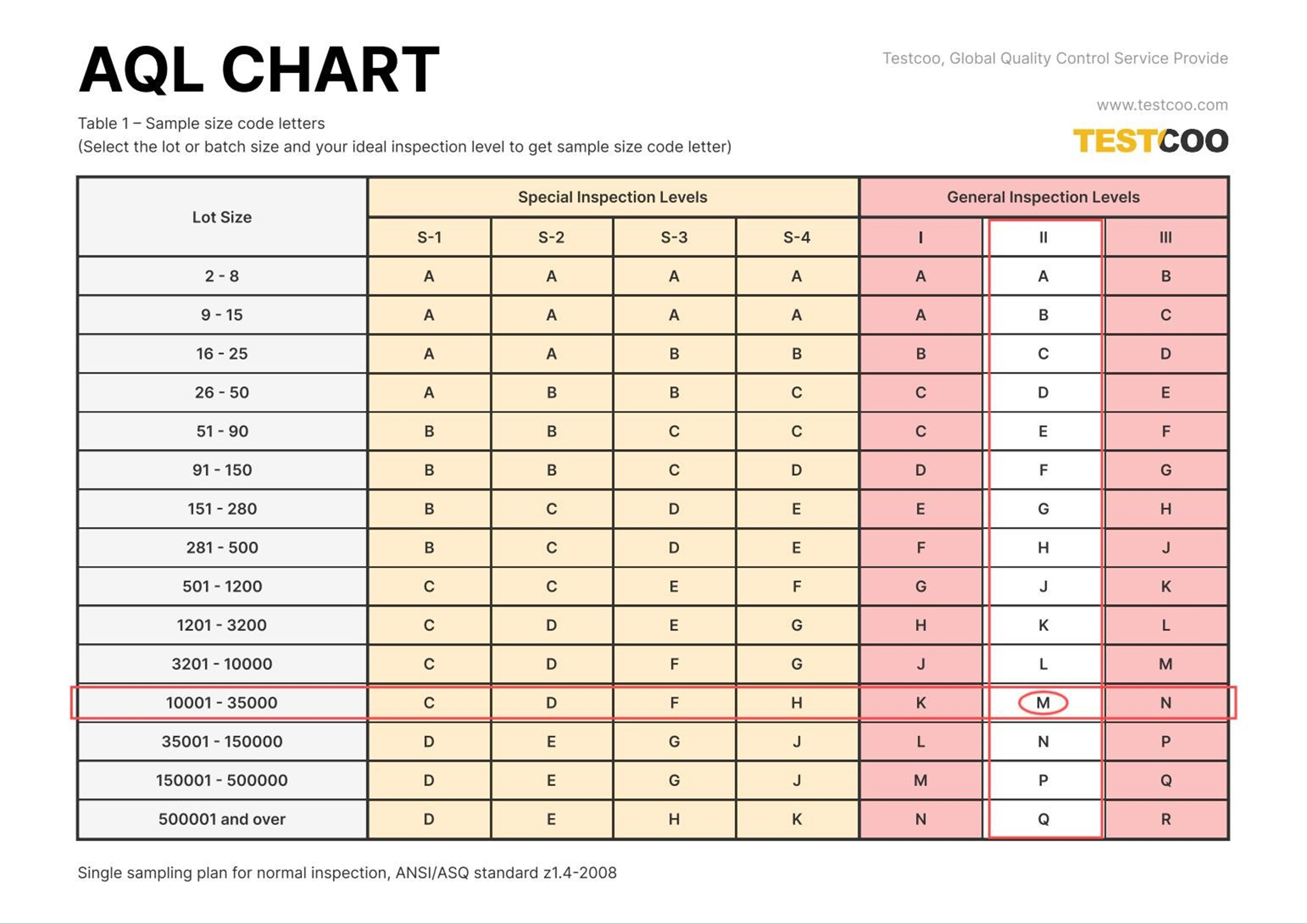
- Step 1: Lot size = 13,000 units, inspection level = II. From Table 1, the sample size code letter is "M".
- Step 2: From Table 2, the sample size corresponding to code letter "M" is 315.
- Step 3:
- Critical defects (0.0%): Any critical defect results in batch rejection.
- Major defects (2.5%): The intersection of row "M" and column "2.5%" shows Ac=14, Re=15. The batch is accepted if major defects ≤14; rejected if ≥15.
- Minor defects (4.0%): The intersection of row "M" and column "4.0%" shows Ac=21, Re=22. The batch is accepted if minor defects ≤21; rejected if ≥22.
Frequently Asked Questions (FAQs)
- What is AQL sampling inspection?
AQL sampling inspection is a statistical method used to infer whether the quality of an entire batch of products meets acceptable standards through sampling in mass production.
- How to use AQL standard tables?
First, determine the sample size based on the lot size and inspection level, then determine the acceptance and rejection criteria based on the AQL value, and finally conduct sample inspection.
- How to set the AQL value?
The AQL value is set through negotiation between the producer and the customer, usually selected based on the product's quality requirements. A lower AQL value indicates higher quality requirements.
- What are the advantages of AQL sampling inspection?
AQL sampling inspection can reduce inspection costs, improve inspection efficiency, and ensure that product quality meets standards.
- How to determine the sample size?
The sample size is determined from the AQL standard tables based on the lot size and inspection level; larger batches usually require more samples.
- Which industries are AQL standards applicable to?
AQL sampling inspection is widely used in quality control in various industries such as manufacturing, electronics, consumer goods, and apparel.
Read More: Frequently Asked Questions about AQL
???????
Free Sample Report Performance Quality Control
Download a sample report to keep control of your supply chain!
Featured Articles
- AQL Table | How to Read It
- TOP 10 Common Defects in Garments Quality Inspection
- Product Packaging and Shipment Label requirements for Amazon FBA
- What Is ASTM-F2413-18? Protective Footwear Standard
- How to Conduct Third-Party Quality Control Inspections for Electric Scooters
- SMETA Audit-What is SMETA Audit?
- TESTCOO Supplier Verification/Certification Service SLCP, Higg FEM, GRS, GOTS
- Quality Control Inspection Company in China
- What is Quality Inspection? A Complete Guide
- Guidelines for Product Inspection in India
Category
- Production Inspection Service
- Factory Audit
- Softline Inspection
- Hardline Inspection
- Electrics Inspection
- Certification
- Checklist
- Manufacturers
- Quality Assurance Basics
- Products Recall
- AQL
- Guidence and Standard
- News
- Supplier Management
- Amazon
- Protective Equipment
- e-commerce quality control
- Indian Manufacturing
- Soft Goods Quality Control
- Supply Chain Management
- Supply Chain Resilience
- E-Commerce Quality Control
- ISO 2859
- Supply Chain Optimization
- Garment Industry
- Higg Index