How to Choose Reliable Wholesale Suppliers in India: A 5-Step QC Guide
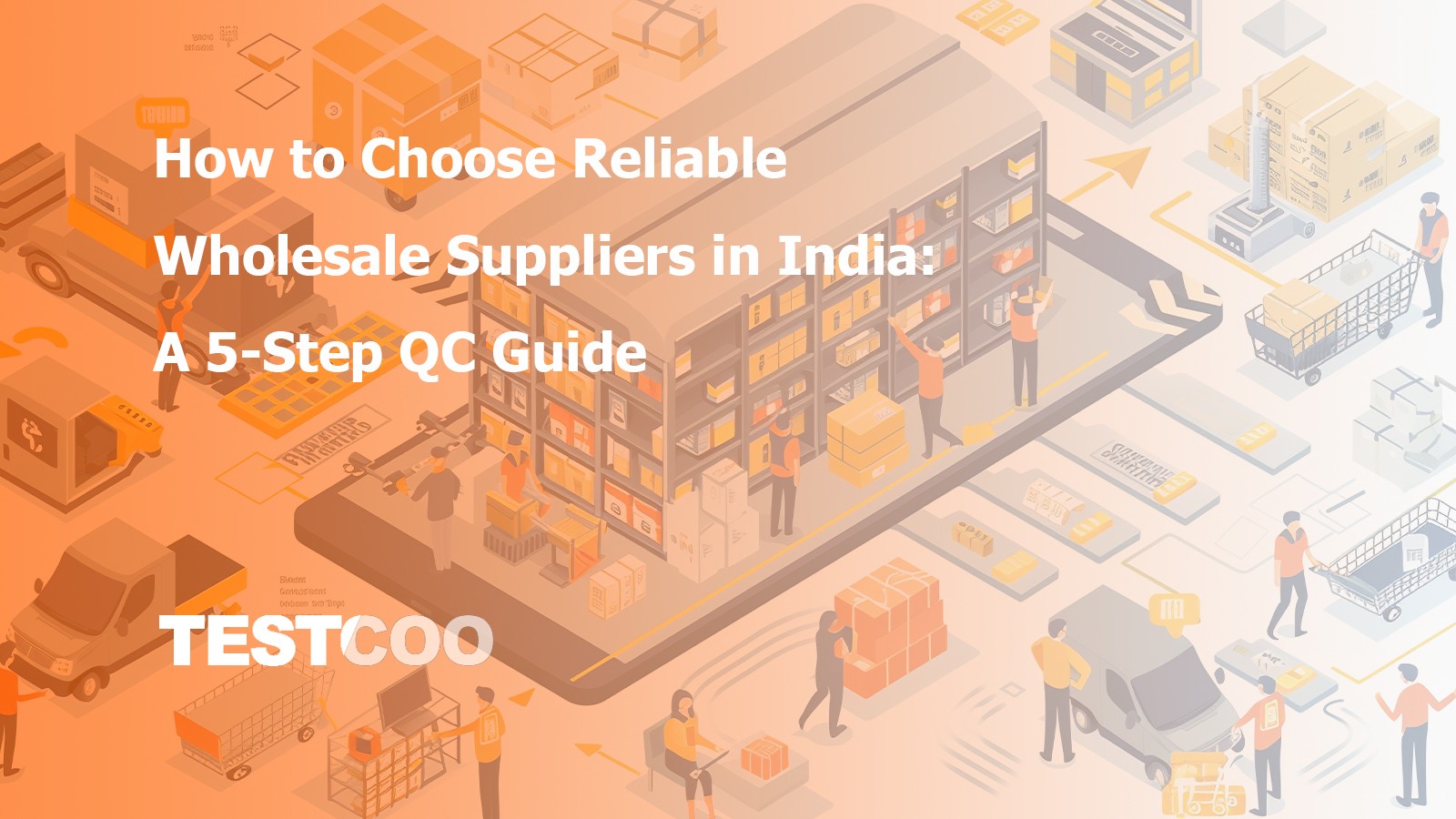
For global importers, sourcing wholesale products from India presents a dual challenge: unlocking competitive pricing while ensuring quality and reliability. Quality and reliability are indeed the key issues when sourcing wholesale products from India. India is a major global sourcing hub, offering a wide range of products from various industries such as textiles, handicrafts, and electronics. However, the diverse and sometimes unregulated business environment means that finding reliable suppliers is no easy task. This is where a comprehensive quality control guide becomes essential.
In this article, we will walk you through a 5-steps quality control (QC) guide that can help you choose reliable wholesale suppliers in India, ensuring that you can build a successful and sustainable business relationship.
Step 1: Top B2B Platforms to Pre-Screen Reliable Wholesale Suppliers in India
Begin your search by leveraging well-established B2B platforms. These platforms have already done some initial vetting of the suppliers, which can save you a significant amount of time and effort.
- IndiaMART: India’s largest hub for manufacturers, featuring verified suppliers across textiles, electronics, and handicrafts.
- TradeIndia: Specializes in industrial machinery and components, with detailed company profiles.
- Udaan: Focused on domestic B2B wholesale, ideal for fashion, lifestyle, and consumer goods.
Screening Tips:
- Look for "Verified Supplier" badges and third-party certifications (e.g.ISO 9001).
- Analyze company metrics: years in business, response rates, and buyer reviews (e.g.a supplier with 10+ years and 4.5/5 ratings signals stability).
- Scrutinize product catalogs for consistency—avoid sellers with generic listings or missing contact details.
- Shortlist 5–10 suppliers with clear communication and detailed product specs.
Red Flag: Suppliers who delay providing basic information or use generic email domains (e.g.@gmail.com) over company domains.
Read More: Guidelines for Product Inspection in India | TESTCOO
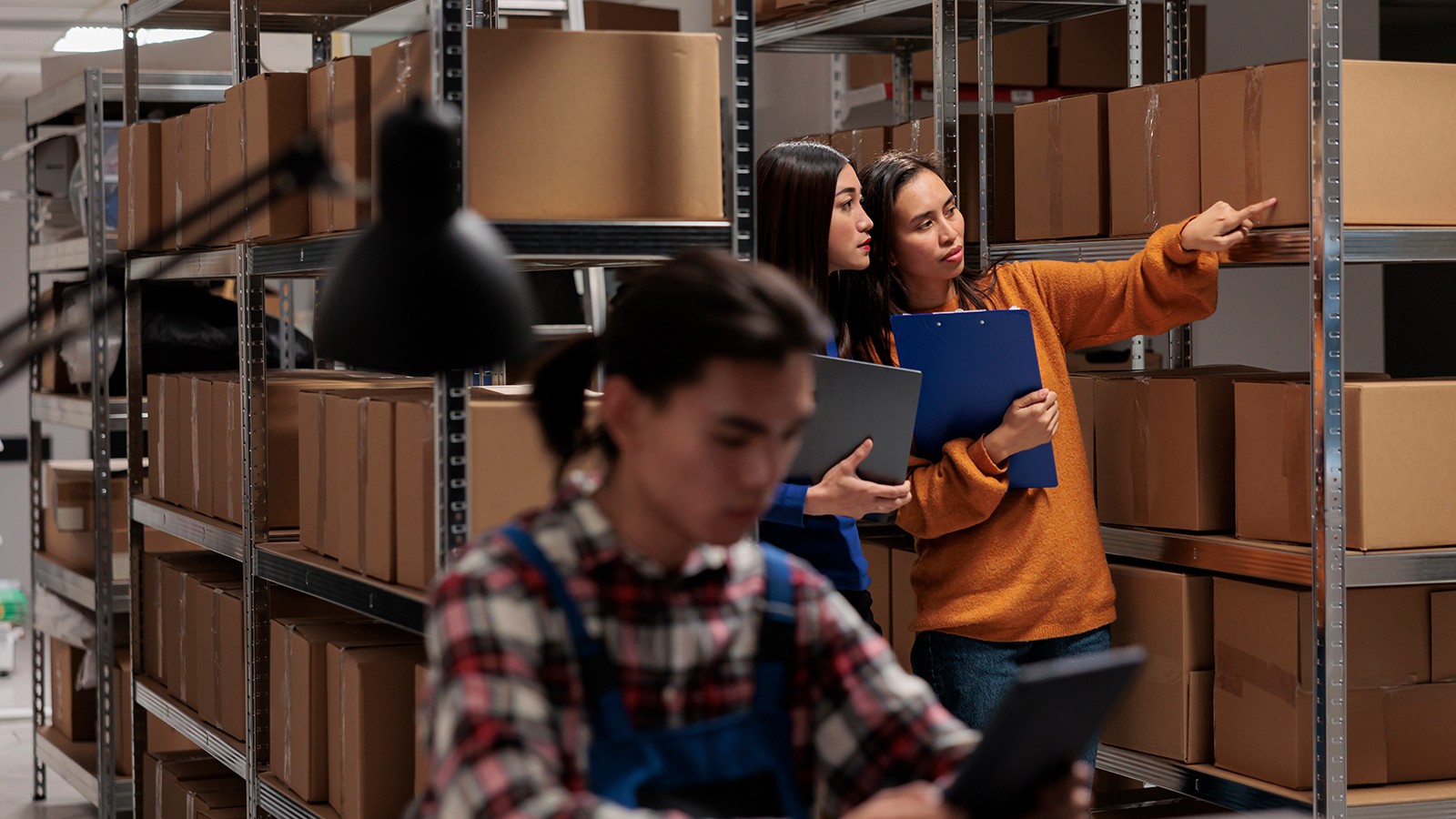
Step 2: Background Verification to Avoid Scams and Fake Manufacturers
Once you have shortlisted 5-10 suppliers from the initial screening on trusted platforms, conducting a background check is crucial. This step is like a safety net that helps you avoid potential scams and unreliable suppliers.
There is a wealth of information that you need to verify about each shortlisted supplier:
- Business License and GST Registration: lid business license is a fundamental requirement. It serves as proof that the business is legally operating in India. Additionally, Goods and Services Tax (GST) registration is essential as it indicates that the supplier is compliant with the country's tax regulations. You can ask the supplier to provide copies of these documents, and then you can verify them through the official Indian government business databases, such as the Ministry of Corporate Affairs website.
- Export License: If you are an international buyer, an export license is a must-have for the supplier. This license ensures that the supplier has met all the necessary requirements to legally export goods from India. Without an export license, there could be significant delays or even legal issues when trying to ship the products out of the country.
- Company Registration Number and Legal Name: The company registration number uniquely identifies the business in the Indian corporate registry. Verifying this number can help you confirm the company's existence and its legal standing. Also, make sure the legal name used by the supplier matches the name on all official documents. Any discrepancies here could be a sign of trouble.
- Factory Location vs. Office Location: It's important to know whether the factory where the products are manufactured is the same as the office location. In some cases, trading companies may pose as manufacturers, which can lead to issues in terms of quality control and production transparency. If the factory and office are in different locations, you need to understand the logistics and communication channels between them.
Third-Party Support:
Services like Testcoo’s on-site audits validate documents and visit premises within 48 hours in hubs like Delhi and Mumbai, and also assess the overall business operations.
Warning Signs
When conducting the background check, be on the lookout for the following red flags:
- Reluctance to share legal docs or frequent name/address changes.
- Unprofessional communication (e.g.broken English, evasive responses to direct questions).
Step 3: Factory Audits: What to Check On-Site Before You Order
In the Indian sourcing landscape, it's alarmingly common for trading companies to pose as manufacturers. These trading companies may not have their own production facilities but instead source products from various small-scale producers and then resell them. This can lead to a lack of control over the production process, resulting in inconsistent product quality.
Even some legitimate factories in India often outsource part of their production to sub-suppliers. This practice is sometimes necessary for factories to meet high production demands or to take advantage of cost-effective production in certain regions. But it also brings risks. Sub-suppliers may not follow the same quality control standards as the main factory.
A factory audit is a crucial step to verify several important aspects of a supplier:
- Manufacturing Capability: Evaluate machinery (e.g.textile mills need automated looms), workforce size, and production progress.
- Production Capacity: Can the facility handle your order volume? Ask for recent production schedules.
- Quality Management Systems: Check for ISO certifications, QC checkpoints, and staff training records.
- Labor and Safety Compliance: Ensure labor practices and safety standards align with global norms (critical for brands with ESG requirements).
Testcoo offers factory audits within 48 hours in key Indian hubs such as Delhi, Mumbai, Tirupur, Jaipur, and Moradabad. Their quick response time allows you to get the information you need in a timely manner, enabling you to make informed decisions about whether to proceed with a particular supplier. With Testcoo's local teams in these key areas, they can conduct in-depth audits, taking into account the local business environment and regulations, which is crucial for a comprehensive assessment of the supplier's capabilities and compliance.
Read More: ISO - ISO 9000 family — Quality management
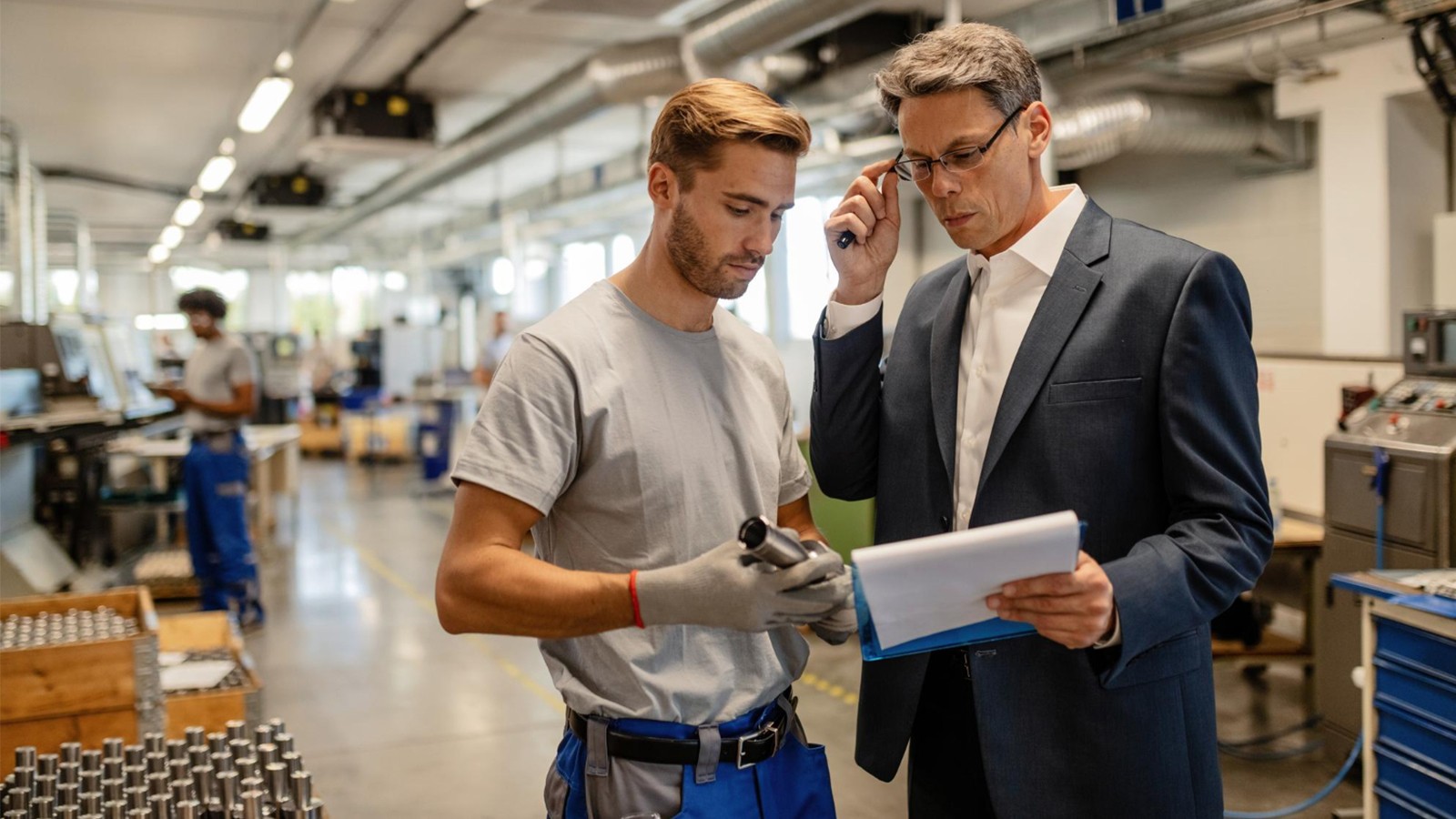
Step 4: Ensure Product Alignment with Initial Production Check
Before mass production commences, running a Initial Production Check (IPC) is a critical step that cannot be overlooked. This step serves as a litmus test for the supplier's ability to meet your exact specifications. By thoroughly examining samples, you can identify any potential issues early on and prevent costly mistakes during large-scale production.
A comprehensive sample review process should cover the following key areas:
- Physical Inspection: Check materials, finish, and functionality against your specs (e.g., fabric weight for garments, circuit testing for electronics).
- Lab Testing: For compliance with standards like REACH (EU), CPSIA (US), or ASTM, use accredited labs (Testcoo offers 72-hour turnaround on tests).
- AQL Standards: Apply Acceptable Quality Limit (e.g.AQL 2.5 for minor defects) to objectively evaluate samples, reducing subjectivity.
A useful tool in evaluating samples is the Acceptable Quality Limit (AQL) standards. AQL provides a systematic way to evaluate samples based on defect types, which are classified as minor, major, or critical. Minor defects may not significantly affect the product's functionality but can impact its appearance or minor features.
Step 5: Final Random Inspection to Catch Defects Before Shipment
Even the most reliable suppliers can make mistakes. In the complex process of production, there are numerous factors that can potentially lead to issues with the final products. Here are the key aspects that should be thoroughly checked during the pre-shipment:
- Conformity to Specifications: Every detail of the product should be in line with the pre-agreed specifications. This includes accurate measurements. For example, if you are importing furniture, the length, width, and height of the tables and chairs should match the dimensions specified in the contract. The labeling on the products must also be correct.
- Packaging Quality: The integrity of the packaging is crucial. The boxes should be in good condition, without any signs of damage, such as tears or dents. The sealing of the packages should be proper to prevent the products from being exposed or damaged during transportation. Barcode accuracy is also important. Incorrect barcodes can lead to issues in inventory management and product tracking.
- Carton Drop Tests: These tests simulate the shocks that the products may experience during shipping. By dropping the cartons from a certain height, you can assess whether the packaging is sufficient to protect the products. In the case of fragile items like glassware or electronics, a failed carton drop test could indicate that the packaging needs to be improved to prevent breakage during transit.
- Functional Tests: For products with moving parts or specific functions, such as electronics, zippers on clothing, or mechanical devices, functional tests are essential. In the case of electronics, all the functions, such as charging, operation of buttons, and connectivity, should be tested.
- Quantity Confirmation: It's essential to verify that the shipment contains the correct quantity of products as per the order. Shortages can disrupt your business operations, especially if you have pre-sold the products or have a tight inventory schedule. Overages can also cause issues, such as additional storage costs or difficulties in accounting for the extra items.
Testcoo offers a highly comprehensive final inspection service. A standard Final Random Inspection (FRI) includes over 100 checkpoints, covering all the aspects mentioned above and more. After the inspection, you will receive a detailed report within 24 hours. This report contains photos of any defects found, a clear classification of defect types (minor, major, or critical), and a PASS/FAIL status. The photos provide visual evidence of the issues, making it easier for you to understand the problems and communicate them to the supplier. The defect classification helps you prioritize the issues and decide on the appropriate actions.
Build Trust Through Testcoo Quality Control
India offers a vast array of products at competitive prices, making it an attractive sourcing destination for global importers. From the vibrant and colorful textiles in cities like Tirupur to the intricate handicrafts and jewelry in Jaipur, the country has a rich manufacturing base. However, quality assurance is of utmost importance when sourcing from India. Cutting corners on quality control can lead to significant financial losses, damaged business relationships, and harm to your brand's reputation.
By following this 5-step QC guide, you can effectively reduce risks in your sourcing process. The initial screening on trusted platforms helps you narrow down the vast pool of suppliers to a more manageable and potentially reliable group. Conducting background checks ensures that you are dealing with legitimate businesses. Factory audits provide in-depth insights into the production capabilities and quality management systems of the suppliers. Final Random Inspection (FRI) allow you to verify the supplier's ability to meet your specifications before mass production, and final product inspections before shipment act as the last safeguard to ensure the products are of the right quality.
Testcoo, as a leading third party quality control company, can be your one-stop solution in this process. With its services including factory audits, product inspections, lab testing, and certification, Testcoo can help you at every step of choosing and verifying Indian wholesale suppliers. Their local presence in India enables them to quickly and effectively assess suppliers, providing you with accurate and timely information.
If you are in the process of sourcing products from India and need assistance in choosing or verifying wholesale suppliers. Contact us to discuss your specific requirements or request a sample report to see the level of detail and quality of their services.
Free Sample Report Performance Quality Control
Download a sample report to keep control of your supply chain!
Featured Articles
- AQL Table | How to Read It
- TOP 10 Common Defects in Garments Quality Inspection
- Product Packaging and Shipment Label requirements for Amazon FBA
- What Is ASTM-F2413-18? Protective Footwear Standard
- How to Conduct Third-Party Quality Control Inspections for Electric Scooters
- SMETA Audit-What is SMETA Audit?
- TESTCOO Supplier Verification/Certification Service SLCP, Higg FEM, GRS, GOTS
- Quality Control Inspection Company in China
- What is Quality Inspection? A Complete Guide
- Guidelines for Product Inspection in India
Category
- Production Inspection Service
- Factory Audit
- Softline Inspection
- Hardline Inspection
- Electrics Inspection
- Certification
- Checklist
- Manufacturers
- Quality Assurance Basics
- Products Recall
- AQL
- Guidence and Standard
- News
- Supplier Management
- Amazon
- Protective Equipment
- e-commerce quality control
- Indian Manufacturing
- Soft Goods Quality Control
- Supply Chain Management
- Supply Chain Resilience
- E-Commerce Quality Control
- ISO 2859
- Supply Chain Optimization
- Garment Industry
- Higg Index