How ‘Make in India’ is Transforming Product Quality Control: Challenges and Opportunities for Brands and Inspectors
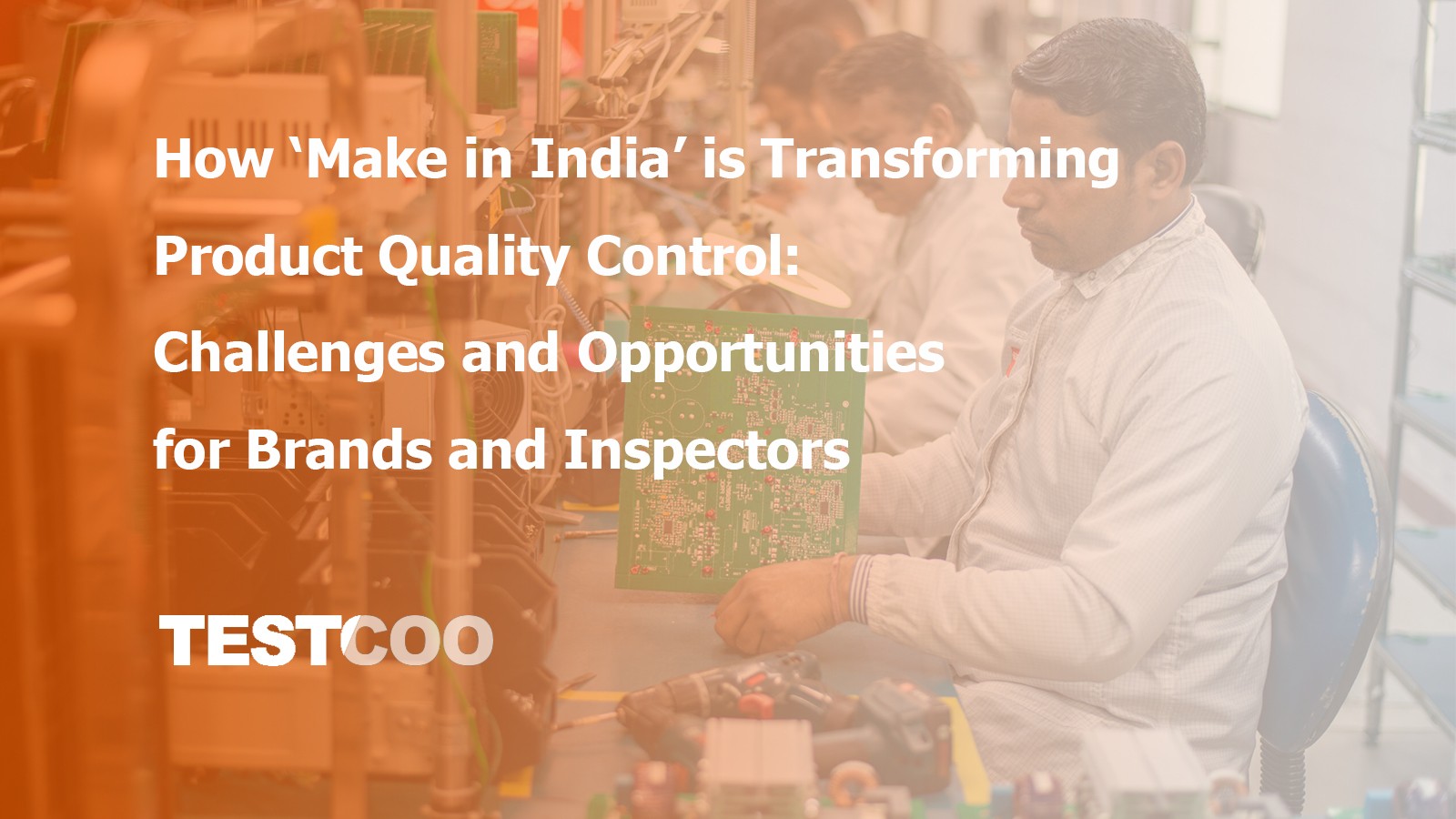
?
Over the past decade, India has emerged as one of the world’s fastest-growing manufacturing hubs. Driven by the ambitious ‘Make in India’ initiative, the country is steadily positioning itself as a trusted sourcing destination for global brands across industries from apparel and textiles to electronics, automotive parts, handicrafts and more.
Yet, with this surge in production and exports comes an equally critical demand: maintaining consistent product quality that meets international standards. For global brands sourcing from India, ensuring product quality isn’t optional, it’s essential for customer satisfaction, brand reputation and market competitiveness.
In this article, we explore how ‘Make in India’ is transforming the landscape of product quality control, the unique challenges manufacturers and buyers face and how third-party inspection companies help bridge the gap ensuring that ‘Made in India’ truly means quality assured.
India’s Manufacturing Boom: A Snapshot
India’s manufacturing sector contributes nearly 17% to the country’s GDP and employs millions across urban and rural regions. Government policies like ‘Make in India’ and ‘Production Linked Incentives (PLI)’ have fueled a wave of investments in manufacturing infrastructure, technology and exports.
Key highlights:
- Textiles & Apparel: India is among the top textile and garment exporters globally, supplying major retail brands in the US, EU and Asia.
- Electronics: India aims to become a global electronics manufacturing hub, with significant production in mobile phones, consumer gadgets and components.
- Handicrafts: The country’s rich artisan heritage drives exports of handicrafts, home décor and handmade products to niche international markets.
- Automotive Parts: Indian auto component makers supply to leading global OEMs.
With this massive scale and diversity, robust quality control processes are vital for India to retain its competitive edge and deliver products that meet or exceed global buyer expectations.
Indian Manufacturing - What Brands Should Consider?
The Unique Quality Control Challenges in India
While India’s manufacturing ecosystem has made impressive strides, it still faces unique challenges that can affect product quality:
Diverse Supplier Base
India’s supply chains include everything from small family-owned workshops to large factories with advanced machinery. This diversity often means varying degrees of process standardization and quality awareness.
Inconsistent Processes
Many small and medium enterprises (SMEs) still rely on manual or semi-automated processes. Lack of documented standard operating procedures (SOPs) can lead to inconsistencies in production output.
Skill Gaps
Despite an abundant workforce, skill levels can vary widely, especially in labor-intensive sectors like textiles, handicrafts or assembly operations. Inadequate training can result in avoidable defects.
Cultural and Communication Gaps
Brands working with Indian suppliers often encounter communication challenges due to language barriers, different work cultures and varying expectations about timelines and specifications.
Common Defects Across Key Sectors
Some of the common defects found in a routine inspection process in various type of products are below:
- Apparel & Textiles: Color shading, fabric flaws, incorrect labeling, loose threads, poor stitching.
- Electronics: Functional defects, poor soldering, non-compliance with safety standards, inadequate packaging.
- Handicrafts: Finish inconsistencies, fragile items damaged during handling or shipping.
Without regular quality checks, these issues can lead to delayed shipments, costly rework or worse, customer complaints and returns that damage brand reputation.
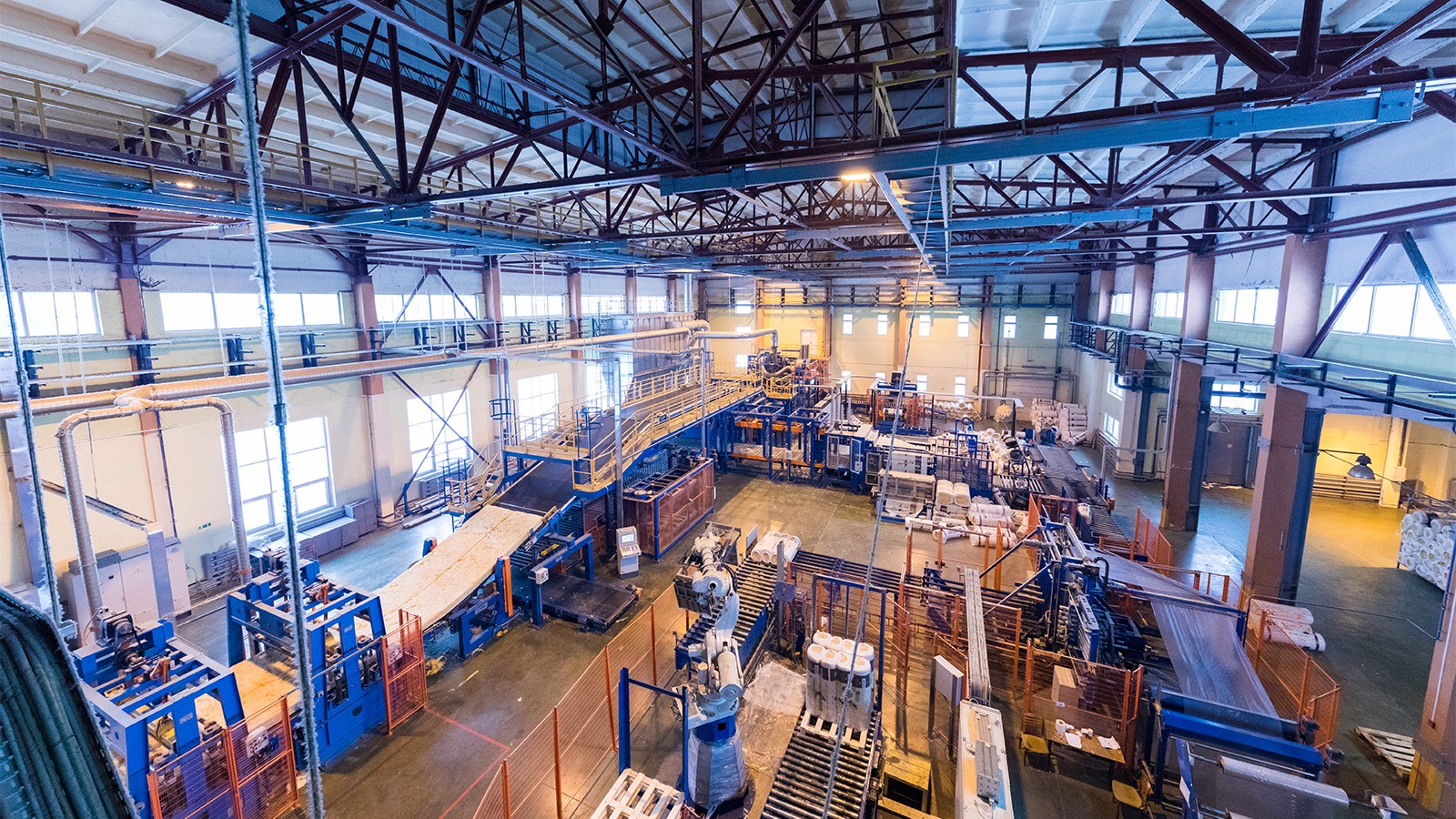
How Third-Party Inspection Bridges the Gap
So, how do global brands safeguard product quality when sourcing from India’s vast and varied manufacturing landscape? This is where independent third-party inspection companies come in.
A reputable inspection partner acts as your eyes and ears on the ground ensuring that what’s produced in the factory matches the agreed standards before it leaves the production floor.
Key Ways Inspections Add Value
Neutral, Unbiased Assessments - Third-party inspectors provide an independent evaluation free from supplier influence, so brands receive transparent, factual reports about their products’ condition and compliance.
Localized Expertise - Experienced inspection teams understand local production practices, regional nuances and typical defect patterns. This allows them to spot potential problems early and recommend corrective actions.
End-to-End Quality Control - Inspection services can cover every stage of production:
- Initial Production Checks (IPC): Verify raw materials and production readiness.
- During Production Inspections (DUPRO): Monitor output quality during manufacturing.
- Final Random Inspections (FRI): Check finished goods before shipment.
- Loading Supervision (LS): Ensure only approved goods are shipped.
Risk Reduction - By catching defects early, brands can avoid costly returns, rework and shipment delays protecting profit margins and brand reputation.
Innovation in Product Quality Control
Today’s quality control is not what it was a decade ago. Technology is transforming inspections, making them faster, more transparent and more reliable.
Digital Reporting
Gone are the days of handwritten checklists and delayed updates. Modern inspectors use mobile devices to record findings in real time, complete with photos, videos and digital signatures delivering same-day reports to clients.
Remote Inspections
Travel restrictions during the pandemic accelerated the adoption of remote inspections and virtual factory audits. Brands can now oversee inspections live via video calls or recorded footage, reducing travel costs and carbon footprints.
Data-Driven Quality Improvement
Some inspection companies use analytics to spot trends identifying recurring defect types or non-compliant suppliers so brands can take corrective action proactively.
Training & Capacity Building
Forward-thinking inspection firms invest in training local inspectors, equipping them with updated knowledge about international standards, customer-specific requirements and industry best practices.
Discover the Guidelines for Product Inspection in India
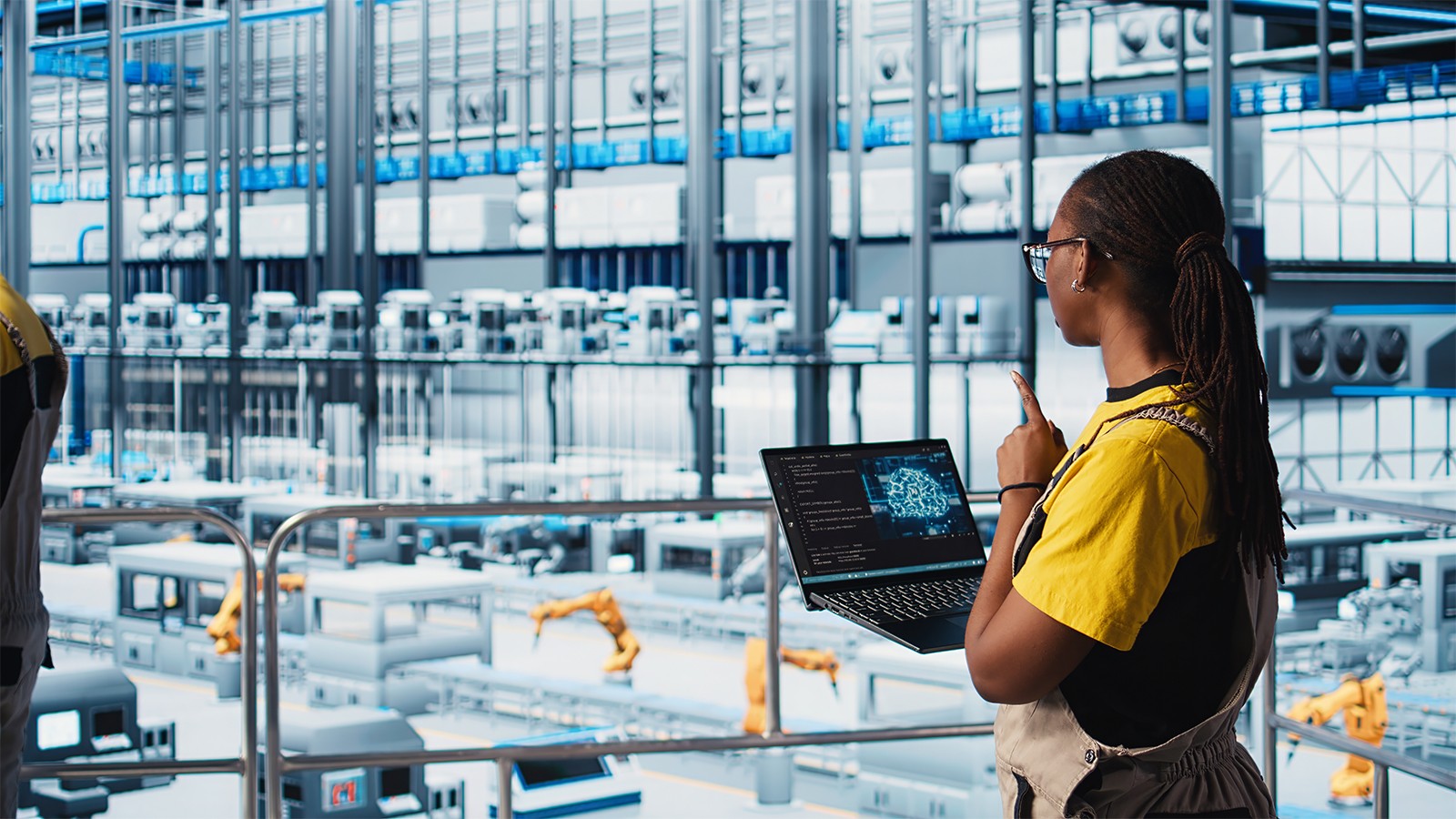
???
Tips for Brands: Getting Quality Right in India
While inspections play a critical role, brands must also build strong foundations for quality control when sourcing from India. Here’s how:
Choose the Right Suppliers - Work with suppliers who have a proven track record, clear SOPs and certifications relevant to your product category.
Define Clear Quality Standards - Communicate specifications, defect tolerances and packaging instructions in writing. Visual references, such as approved samples, help avoid misunderstandings.
Develop a Robust Inspection Plan - Plan for inspections at multiple stages not just the final check. Early detection minimizes surprises and gives suppliers time to fix issues.
Use a Customized Inspection Checklist - Each product category has unique checkpoints. A good inspection partner will develop a detailed checklist tailored to your specifications and AQL (Acceptable Quality Limit).
Insist on Transparent Reporting - Your inspection partner should provide clear, unbiased and timely reports, so you can make informed shipment decisions.
Build Long-Term Relationships - Working with the same inspection partner builds trust and consistency. They learn your product requirements deeply, which results in more accurate inspections.
Opportunities Ahead: Why Quality Will Define India’s Next Leap
As India aims to boost its share of global exports, quality will be a key differentiator. Major global brands increasingly demand not just cost-effective manufacturing but also:
- Consistent product quality
- Ethical and social compliance
- Sustainable production practices
Third-party inspection companies are evolving alongside these demands expanding their services to include sustainability audits, ethical sourcing checks and supplier training.
In this new era, robust quality control is not just a safeguard; it’s a strategic advantage that helps Indian manufacturers earn repeat business, attract high-value buyers and strengthen ‘Made in India’ as a mark of quality.
Ready to Protect Your Brand?
India’s ‘Make in India’ mission has unlocked remarkable opportunities for manufacturers and brands alike. But as global demand grows, so does the need for unwavering quality.
Partnering with a trusted third-party inspection company ensures your products consistently meet international standards, reduce costly surprises and strengthen your brand’s reputation in the eyes of customers worldwide.
At Testcoo, we’re proud to support brands sourcing from India with reliable, efficient and customized inspection solutions. Whether you’re shipping garments to Europe, electronics to the US or handcrafted products to niche markets, our experienced teams are here to help you deliver quality every time.
Connect with us today to discuss how our on-ground inspection and audit services in India can support your supply chain, reduce risks and help you grow with confidence
Related Articles
Read MoreFree Sample Report Performance Quality Control
Download a sample report to keep control of your supply chain!
Featured Articles
- AQL Table | How to Read It
- TOP 10 Common Defects in Garments Quality Inspection
- Product Packaging and Shipment Label requirements for Amazon FBA
- What Is ASTM-F2413-18? Protective Footwear Standard
- How to Conduct Third-Party Quality Control Inspections for Electric Scooters
- SMETA Audit-What is SMETA Audit?
- TESTCOO Supplier Verification/Certification Service SLCP, Higg FEM, GRS, GOTS
- Quality Control Inspection Company in China
- What is Quality Inspection? A Complete Guide
- Guidelines for Product Inspection in India
Category
- Production Inspection Service
- Factory Audit
- Softline Inspection
- Hardline Inspection
- Electrics Inspection
- Certification
- Checklist
- Manufacturers
- Quality Assurance Basics
- Products Recall
- AQL
- Guidence and Standard
- News
- Supplier Management
- Amazon
- Protective Equipment
- e-commerce quality control
- Indian Manufacturing
- Soft Goods Quality Control
- Supply Chain Management
- Supply Chain Resilience
- E-Commerce Quality Control
- ISO 2859
- Supply Chain Optimization
- Garment Industry
- Higg Index